Biomass Briquetting Plant Cost and Market
International Market of Briquetting Production: Part of the Kyoto protocol’s key objectives was to ensure that different countries all over the world benefit from the wonders of this alternative fuel. Here is the impact it has had thus far.
Global Regulation Through the Kyoto Protocol
The use of biomass molding fuel is not exactly new. However, it became a global phenomenon in the 21 st century. As an industry, it has been experiencing incredible growth with a projected market value of around 570 million USD by 2015. With so much hanging on the line, key international players came together to formulate rules and guidelines to ensure the world benefits equally from this new energy source. These were compiled in what is known as the Kyoto protocol. The main aim was to oversee fuel replacement projects where biomass briquettes were used in place of traditional fuels.
Briquette Market In Developing Countries
This includes countries in Africa and some parts of Asia. With the help of both government and non-governmental organizations, the use of biomass fuel has been adopted in both industrial and domestic scale. Here is a list of some of the countries that have made the biggest strides forward.
- Democratic Republic of Congo
Major progress was achieved through collaboration with The Legacy Foundation. The change involved creating awareness at grassroots levels and getting rural dwellers interested in making their own biomass. This replaced fuels like wood and charcoal as the main source for basic household energy needs like cooking.
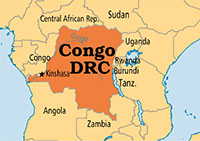
- Tanzania
A region in Tanzania known as Pangani has been a national inspiration in their adaptation of biomass energy models. The area is known for its expansive coconut groves. After harvesting season, the place is pretty much a raw material factory for biomass molding fuel with husks, coconut cases and much more. After being made aware of what they were sitting on, residents took up molding as a serious venture. They are now reaping the fruits of their hard labor as Pangani is one of Tanzania's leading sources of briquettes.
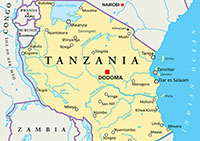
- Africa's great lake region
This includes Kenya, Uganda and Tanzania. The national governments in these 3 countries worked with NGOs, the EU and Dutch national government to spearhead biomass projects. The five year plan saw successful adoption of this alternative source in numerous companies and households.

- India
India has been a force to reckon with as far as biomass molding fuel is concerned. The most effect can be seen industrially with briquette’s being among the country's most popular sources of fuel for heat generation in major companies.
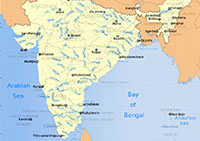
Briquette Market In Developed Countries
There has also been major progress noted in developed countries. For the most part, these major world economies contributed largely to the carbon emission burned that plagued the world. Their adoption of safer and cleaner fuels like biomass briquettes has therefore had a huge impact.
- United States
Take the United States for instance. It has been singled out as the largest emitter of carbon waste from fuel in the world. However, the country is cleaning this record by adopting green fuel options including biomass briquettes.
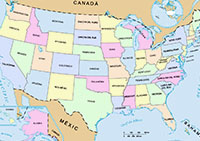
- Arizona
A great example is a campaign in the state of Arizona to take bio waste off the hands of farmers and use it to make fuel to run industries. This includes waste from animal farms, cotton plantations and many others. The move has proven to be a massive success this far offering a more environmentally friendly fuel option while getting rid of the unwanted.
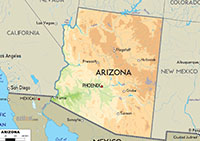
Biomass Briquetting Plant Cost Analysis
Before running a briquetting plant, the cost must be your first concern. There are a number of factors that will determine the overall financial costs of briquetting including the location of the plant and the applied raw material. The costs can be categorized into two groups: capital costs and operational costs. The economic viability of briquetting at a certain location is largely dependent on how these costs relate to the substitute fuels' prices. Herein is a brief overview of factors that can influence the financial costs of briquetting.
Capital Costs
Establishing the capital costs of a briquetting plant is not always a straightforward process. In some cases, there is a lack of general consensus on what exactly should be included as part of capital costs. For instance, spare parts can be classified as both an operational cost and capital cost depending on the circumstances.
The capital cost of the plant will depend on whether it’s a stand-alone plant or a section of an existing agro plant with available facilities. One major factor that determines the capital costs is the raw material and its form upon collection. The output rate of briquetting machines will vary considerably depending on characteristics of the raw materials such as density.
For instance, wood residues result in higher output than most agro-residues thus incurring lower costs. In other cases, the raw materials may need to undergo pretreatment or other processes such as drying, chipping or shredding before being fed to the briquetter. This will increase the capital cost significantly. One also has to factor in the cost of equipment necessary for the collection of raw materials.
Cypriot Clients of our Punching type Wood Briquetting Plant
The engineering and design of the wood briquetting plant will also affect the capital costs. Spacious buildings are necessary in plants where mechanical handling is minimal or non-existent in order to avoid overcrowding or dustiness. Residue-producing plants where briquetting machines are housed in existing buildings will have lower capital costs.
Operational Cost
The price of the raw material is the first operational cost that a plant will incur. The cost will depend on the location and specific project. In some cases, the residue might be free. However, there is significant transportation costs incurred when moving the material from the field to the briquetting plant. This costs may be avoided if the plant sits in close proximity to the residue production site.
Another operational cost is labor. This will vary greatly depending on the design of the briquetting plant, the workload during revenue collection and the wages of different types of workers. Generally, labor is necessary for supervision, collecting, maintenance and loading. The labor costs may be lowered if the plant is part of a large factory where labor can be supplemented on a part-time basis.
The great news is that labor costs for briquetting take up just a relatively small percentage of the total financial costs. One often underestimated operational cost in briquetting is maintenance costs. Maintenance costs can be significantly high when the briquetting machines are used to process abrasive raw materials such as charcoal or rice husks.
Certain components including screw presses, pan grinders, and piston presses will require regular maintenance or even replacements. Most plants will rely on imported spare-parts, driving up the operational costs.
The power supply is also another variable to consider if the plant lacks manual briquetting machines. This can be in the form of diesel generators, steam/diesel engines, and electricity. The power requirements and consumption rates for each machine are factors that will influence the operational costs.
There are many other costs that must be taken into consideration when running a briquetting plant. These include insurance, taxes, packaging and auxiliary products/services.
Killing Two Birds with One Stone
After years of choking the world with toxic fuel effluents, the focus has finally shifted to cleaner and more sustainable options. One of these is biomass molding fuel. The best thing about this option is that it solves two problems at once. On one hand, we get access to a more convenient and environmentally friendly alternative to traditional fuels. On the other hand this fuel gives us a way to deal with agricultural and forestry wastes. But what exactly is biomass molding fuel?Biomass Molding Fuel: Pellets Vs Briquettes
Depending on the materials, processing methods and compacting tools used, there are two types of biomass molding fuel products. These are pellets and briquettes. Here is a little more about them and what makes each different.
Pellets
Pellets are more often than not made from wood waste. This includes saw dust and shavings from carpentry as well as splinters and broken pieces from lumber mills. In some countries, fruit shells and cases are used including those from palms, coconuts and legumes.
These are dried and compacted into small pellets that are then burnt as fuel. Compared to briquettes, they do not produce a lot of energy and you would need more of the pellets to produce the same amount of energy. Biofuel pellets are therefore commonly applied in low demand tasks like cooking, small scale heat generation and other household needs.
Briquettes
Briquettes are made from green waste and organic matter. This includes things like agricultural waste and bagasse. It is also not uncommon for makers of biomass molding fuel to use animal excrement to make briquettes.
Briquettes are significantly more efficient in production of energy. They therefore come in handy in high-energy-demand situations. A great example here is in electricity generation. In this case, the briquettes are burned and used to heat water into steam. The steam is then used to drive powerful turbines that generate power. In addition to industrial applications, briquettes can also be used as alternatives to gas and electricity for cooking and heating in domestic settings.
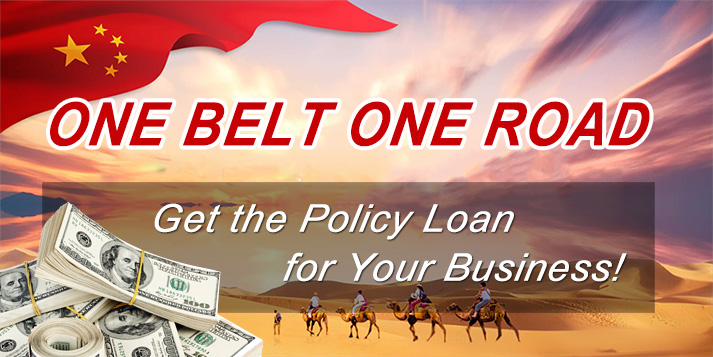
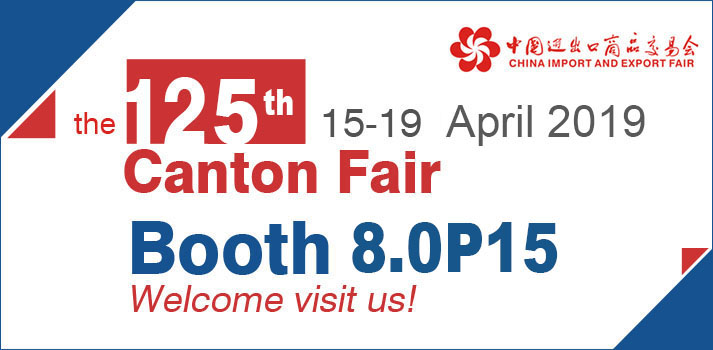
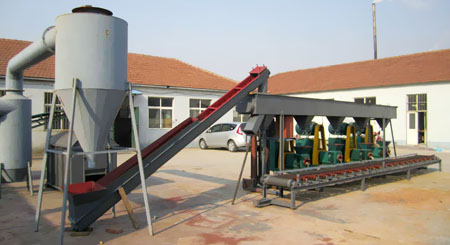
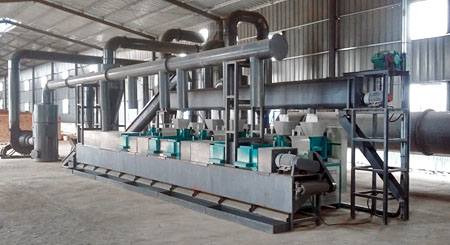
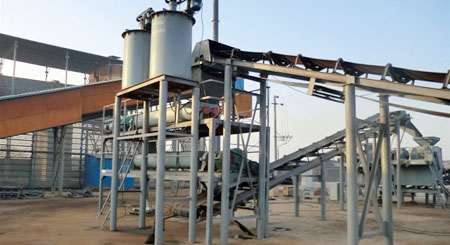